Contact your local Osmose experts about your wood pole inspection and life extension needs.
Wood Utility Pole Inspection and Maintenance
Proper contractual maintenance of wood poles, which includes inspection and application of remedial treatments, helps add many years of safe, reliable service life to your pole plant, thereby reducing unnecessary or premature replacement costs.
The keys to a successful wood utility pole inspection program are:
- Identifying decay & measuring defects
- Estimating the pole’s remaining strength to determine pass/fail - Inaccurate strength calculations can be costly. A false fail can lead to unnecessary spending on restoration or replacement, while a false pass can create a risk that may lead to pole failures and costly damage and repairs. Osmose technicians use StrengthCalc® software which models the cross-section of decaying poles in relation to the transverse loads. StrengthCalc accounts for both the severity and location of the decay with respect to conductors and equipment. StrengthCalc determines precise section modulus to provide the percent remaining strength for weakened poles.
- Applying effective remedial treatments to extend the safe, reliable service life of the pole. Remedial treatment is the key to getting the most out of your investment. The use of remedial treatments will earn dividends via extended pole life and improved plant resiliency.
Methods & Accuracy of Wood Utility Pole Inspections
A vital aspect of maintaining a utility pole is conducting regular pole inspections to evaluate the condition of the wood. To ensure accuracy, various methods are employed to determine the degree of decay or damage present.
One method involves "sounding" the poles with a hammer to indicate suspected internal decay. Boring also may be used to confirm decay in the suspected area and determine the location and extent of internal decay.
To better identify and measure signs of external decay, a partial excavation can be used. The most thorough method involves fully excavating the pole to a depth of 18 inches to determine the extent of decay below the groundline. Any decayed wood is removed, and a preservative paste is applied to protect the remaining sound wood.
For industry best practice, a comprehensive life extension approach is recommended. This includes a full excavation to a depth of 18 inches to identify and measure external decay and sounding and boring the pole to identify and measure internal decay. Decayed wood is removed, and a preservative paste is applied to protect the remaining sound wood.
To ensure the effectiveness of these methods, utility pole inspectors must have field experience and access to appropriate equipment. It is also essential to consider the pole species and the surrounding typical climate when conducting pole assessments, as this can affect the frequency of inspection, level of decay and analysis required. Various pole assessment methods may also be utilized to enhance accuracy and efficiency in identifying internal and external decay , to determine the need for reinforcement or replacement.
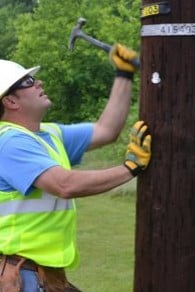
Sound and Selective Bore
✅ Locates obvious rejects quickly with a minimal investment.
⛔ Leaves a considerable number of undetected rejects (along with liability and risk).
⛔ 2-year inspection cycles are recommended.
⛔ Reject rates remain high in future cycles.
⛔ 100% O&M (no life extension means no opportunity to capitalize a portion of the expense).
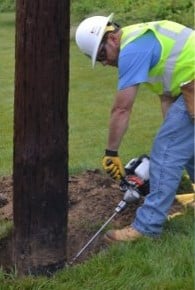
Sound and Bore
✅ Locates obvious rejects quickly with a minimal investment.
⛔ Leaves a considerable number of undetected rejects (along with liability and risk).
⛔ 2-4 years inspection cycles are recommended.
⛔ Reject rates remain high in future cycles.
⛔ 100% O&M (no life extension means no opportunity to capitalize a portion of the expense).
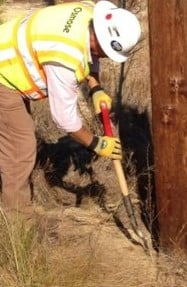
Sound and Bore with Partial Excavation and Selective Treatment
✅ Improved inspection accuracy (because a below-grade portion of the pole is exposed and inspected.
✅ The investment will earn some dividends via extended service of life of treated poles.
✅ The inspection cycle can be extended to 4-6 years.
⛔ Though inspection accuracy is improved, it is not "best practice" and leaves 10%-30% of rejects unidentified.
⛔ Reject rates will be higher on future cycles than those obtainable with a full excavate program.
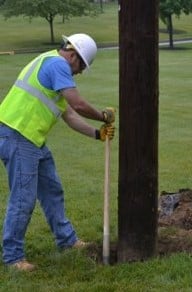
Comprehensive Inspection (Sound, Bore, 10" Excavation, Remedial Treatment)
✅ Most accurate inspection - locates 98% of rejects.
✅ Investment will earn dividends via extended pole life and improved plant resiliency.
✅ Because asset life is extended, owners may choose to capitalize all or a portion of the expense.
✅ Inspection cycle can be extended to 8-12 years.
⛔Increased initial investment
⛔ May take longer to inspect the entire system.
Aerial Services
Osmose is a utility structure expert with 90 years of expertise. Our unique blend of cutting-edge technology, experienced personnel, and in-depth utility structure assessment knowledge sets us apart. Unlike a standard drone service provider, Osmose doesn’t just provide pictures; we provide actionable insights. Our comprehensive report and condition assessment points the way forward, a priceless asset to utilities facing complex decisions.
.jpg)
Get a free, no-obligation consultation with an Osmose pole inspection and maintenance expert.
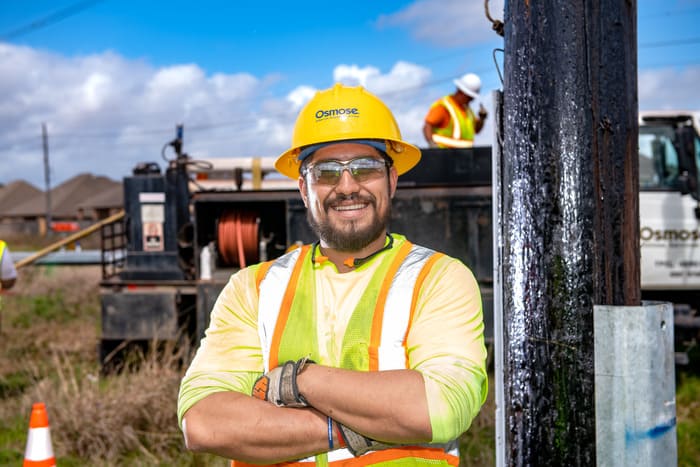
Selecting a Service Provider From a Myriad of Utility Pole Inspection Companies
Utility pole inspections should be handled by inspection and contractual maintenance experts to prevent inaccurate assessments.
Osmose has a proven track record in implementing excellent, value-adding wood pole inspection services. Every Osmose utility pole inspector is equipped to determine fungi decay and other signs of problems using a thorough contractual utility pole maintenance and inspection process.
Wood Pole Inspection Services That Work
Efficient utility pole inspection companies understand the importance of maximizing the investment of pole plant owners. Through Osmose's wood pole inspection and contractual maintenance process, the service and inspection lifecycle of treated poles are extended significantly. From basic wood pole inspection to in-depth power pole repair, Osmose can help you optimize your life-extension investments by matching your program objectives with an appropriate inspection method.