Contact your local Osmose Professional.
Steel Structure Assessment
In the field, Osmose has applied the collective experience of evaluating hundreds of thousands of steel structures in developing a best-in-class approach to structural assessment. Using a current drone and LiDAR scanning technology, together with excavation, structural measurements, and foundation assessments, Osmose engineers examine steel structures at two zones – groundline and above grade.
.jpg)
.jpg)
Osmolytics®
Osmolytics is a predictive analytics platform that leverages empirical data, circuit data, and environmental information to help understand and prioritize the resiliency and capacity of grid structures. Predictive assessments provide an economical and effective approach to target the most detrimental conditions and highest risk structures and circuits.
Comprehensive Field Evaluation
Industry-certified field technicians are trained to assess structures, their foundations, and soil environmental conditions, assigning structural condition ratings and identifying areas of focus.
OsmoDrone - Aerial Assessment
Osmose performs a full structure assessment using FAA-certified pilots while leveraging the latest drone technologies.
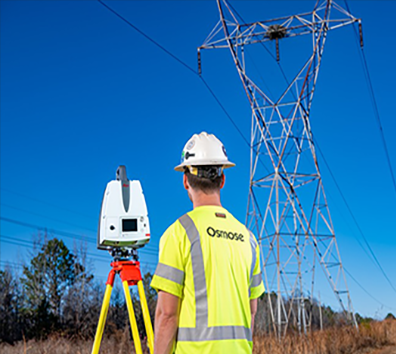
.png?width=396&height=354&name=tower1%20(1).png)
Steel Structure Assessment Case Study
A utility in the Southeast US initiated a pilot assessment project to determine the below-grade condition of their transmission system.